.png)
The Opportunity Cost of Not Adopting BIM
Introduction
Building Information Modeling (BIM) is changing the way the construction industry works. It offers a smarter and more efficient way to design, plan, and manage projects. But for many, the decision to adopt BIM still feels like a big step. This hesitation comes with what we call an "opportunity cost." In simple terms, the opportunity cost is what you lose when you choose not to take a certain action.
In construction, not adopting BIM means missing out on many benefits. These include better collaboration, fewer mistakes, and reduced project delays. By sticking to traditional methods, companies may save money upfront, but they could end up spending much more in the long run. Inefficiencies, design errors, and rework all add up, leading to higher costs over time.
This blog will dive into the true cost of not using BIM. We’ll look at what companies lose by not adopting this technology and how it impacts efficiency, design accuracy, and sustainability. Understanding these opportunity costs can help businesses make better decisions about whether or not to invest in BIM.
What is BIM and Its Benefits?
Building Information Modeling, or BIM, is a digital tool that allows construction professionals to plan, design, and manage building projects with greater accuracy and collaboration. Unlike traditional 2D drawings, BIM creates a 3D model of a building, incorporating detailed data about every component. This helps architects, engineers, and builders work together more effectively.
One of BIM's main benefits is improved collaboration. Everyone involved in the project works from the same updated model, reducing the chances of miscommunication. This leads to fewer mistakes and helps avoid costly rework. BIM also increases efficiency. It automates many parts of the design process, like clash detection, which finds issues between different systems (like plumbing and electrical) before construction even starts. This saves time and prevents delays later in the project.
Another important benefit is cost savings. By catching potential problems early, BIM helps reduce the need for changes during construction. This means fewer surprises, less waste, and more predictable budgets. Finally, BIM supports sustainability. It allows teams to analyze energy use, material waste, and environmental impact, leading to greener buildings.
In short, BIM is more than just a design tool. It’s a system that helps improve efficiency, reduce costs, and promote sustainability in construction.
Understanding Opportunity Cost in Construction
Opportunity cost is a simple concept: it’s what you lose by not choosing a certain option. In construction, the opportunity cost of not adopting BIM can be significant. When companies stick to traditional methods, they might save money upfront, but they miss out on long-term benefits that could save more in the end.
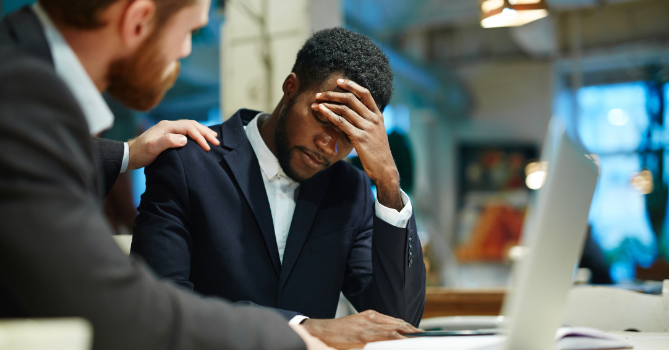
For example, without BIM, teams often face communication breakdowns, leading to delays, errors, and rework. These issues can increase costs over time, making projects take longer and require more resources. In contrast, BIM helps teams collaborate in real-time, reducing these common problems.
Not using BIM also means missing out on efficiency. BIM automates tasks, such as clash detection and scheduling, which traditional methods can’t handle as effectively. This loss of efficiency adds up quickly in both time and money. Additionally, the lack of BIM can hinder a company’s competitiveness. As more businesses adopt BIM, those that don’t risk falling behind, losing out on bigger projects and future opportunities.
In the construction industry, the opportunity cost of not using BIM is high, leading to more delays, errors, and missed opportunities for growth and savings.
Missed Efficiency Gains and Increased Costs
Not adopting BIM in construction leads to missed opportunities for improving efficiency and reducing costs. When teams rely on traditional methods, like 2D drawings and manual updates, they face several challenges that could be avoided with BIM.
One of the biggest efficiency losses is in communication. Without a centralized model, architects, engineers, and contractors often work from different versions of plans. This can lead to miscommunication and confusion, causing errors and delays. These delays are costly, as they extend project timelines and require additional resources to fix the problems.
BIM, on the other hand, provides a real-time, shared model that updates instantly as changes are made. This level of coordination reduces the need for back-and-forth communication and prevents misunderstandings before they happen. It also helps teams make decisions faster, keeping the project on schedule.
Another missed opportunity is in reducing rework. Projects that don’t use BIM often face more design errors and clashes between different systems, like plumbing and electrical. These issues might not be caught until construction is already underway, leading to costly rework. Fixing these problems not only adds to the project budget but also wastes materials and labor.
Furthermore, traditional methods don’t offer the same level of project planning and forecasting as BIM. This makes it harder to predict and manage costs, leading to unexpected expenses as the project progresses. BIM’s detailed models allow for better cost estimation, helping teams stay within budget from the start.
In summary, the decision not to adopt BIM can lead to significant inefficiencies and increased costs. These missed gains in efficiency and the financial burden of errors and delays make traditional methods less cost-effective over time.
Higher Risk of Design Errors and Rework
When projects don’t use BIM, the risk of design errors and rework increases significantly. Traditional methods rely on 2D drawings, which are prone to misinterpretation. Different teams—like architects, engineers, and contractors—often work from separate plans. This lack of coordination can lead to mistakes that only become obvious during construction.
One of the most common issues is system clashes. For example, an HVAC system might conflict with plumbing or electrical layouts. Without BIM’s clash detection feature, these problems aren’t found until construction begins, causing costly rework and delays. Fixing these errors not only adds time but also increases the budget as materials and labor are wasted.
BIM’s 3D modeling and clash detection solve this issue. Teams can spot conflicts early and make adjustments before construction starts. This reduces rework and keeps projects on track. The result is a smoother, more efficient build with fewer unexpected surprises.
By not using BIM, companies risk higher project costs and longer timelines due to these avoidable design errors. This not only affects the project’s bottom line but also impacts client satisfaction and the overall quality of the work.
Lost Sustainability Benefits
Choosing not to adopt BIM also means missing out on significant sustainability benefits. In today’s construction industry, sustainability is more important than ever. Projects need to minimize waste, reduce energy consumption, and consider their environmental impact. BIM plays a key role in achieving these goals.
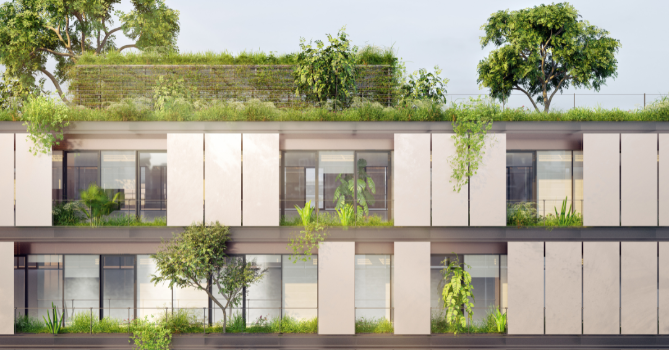
Without BIM, teams often struggle to optimize material use. Traditional methods rely on rough estimates, which can lead to over-ordering or under-utilizing materials. This creates waste, driving up costs and harming the environment. BIM, however, offers precise material calculations, allowing teams to plan exactly what’s needed, reducing waste and improving efficiency.
BIM also enables energy modeling. This feature lets teams analyze how a building will perform in terms of energy use and environmental impact. Without this, projects may miss opportunities to design energy-efficient buildings, leading to higher operating costs and a larger carbon footprint.
By not using BIM, companies lose the chance to design greener buildings and reduce their environmental impact. As sustainability becomes more of a priority in construction, missing out on these benefits can affect a company’s reputation and its ability to meet client demands for eco-friendly projects.
The Long-Term ROI of BIM
Adopting BIM might seem like a large upfront investment, but the long-term return on investment (ROI) makes it worthwhile. BIM helps companies save time, reduce errors, and manage projects more efficiently, leading to significant cost savings over time.
One of the biggest ways BIM boosts ROI is by preventing costly rework. By catching design clashes early, BIM reduces the likelihood of expensive corrections during construction. These savings quickly outweigh the initial investment in the software and training.
BIM also improves project timelines. Faster decision-making and real-time collaboration mean fewer delays, which can be a major cost factor in construction. With projects being completed on time, or even ahead of schedule, companies can take on more work, boosting overall profitability.
Additionally, the sustainability benefits of BIM—such as reduced waste and energy-efficient designs—further increase long-term savings. Buildings designed with BIM are often cheaper to operate, making them more attractive to clients who value sustainability.
In the end, BIM delivers more than just short-term gains. Its ability to improve project outcomes and reduce long-term costs makes it a smart investment for any company looking to stay competitive in the construction industry.
Conclusion
The opportunity cost of not adopting BIM is significant. Companies that stick to traditional methods miss out on improved efficiency, reduced design errors, and the ability to build more sustainable projects. These missed benefits add up, leading to increased project costs, delays, and wasted resources.
BIM offers a long-term return on investment that far outweighs the initial cost. By improving collaboration, cutting down rework, and enhancing sustainability, BIM helps companies save both time and money. In an industry where margins are tight and timelines are critical, those who embrace BIM are better positioned for success.
Choosing not to adopt BIM is a decision that can limit growth, profitability, and competitiveness. Now more than ever, investing in BIM is a smart move for any company looking to stay ahead in the future of construction.