.png)
Modular and Prefabrication Construction: Leveraging BIM for Faster Builds
Introduction
Modular and prefabrication construction methods are growing in popularity for good reason—they save both time and money. By constructing building components offsite and then assembling them on location, projects can be completed more efficiently. This approach reduces waste, speeds up timelines, and limits the disruptions commonly seen with traditional builds.
Building Information Modeling (BIM) has become a vital part of this shift. BIM allows teams to design, visualize, and manage prefabricated elements with a high level of accuracy. This leads to fewer errors during assembly and faster project completion. By using BIM, construction technology is becoming more reliable and precise, making prefabrication a smarter option for many projects. With BIM driving efficiency, modular construction is positioned to reshape the future of building.
How BIM Enhances Modular and Prefabrication Construction
Building Information Modeling (BIM) greatly enhances the design phase of modular and prefabrication construction. By creating detailed 3D models, BIM allows project teams to visualize every component before construction begins. This level of visualization helps teams plan more effectively, improving precision in the prefabrication process. Designs can be refined early on, reducing errors that might arise during assembly. One key benefit of BIM is its ability to detect clashes between different building systems before manufacturing even starts. This early clash detection saves time, reduces rework, and keeps projects on track.
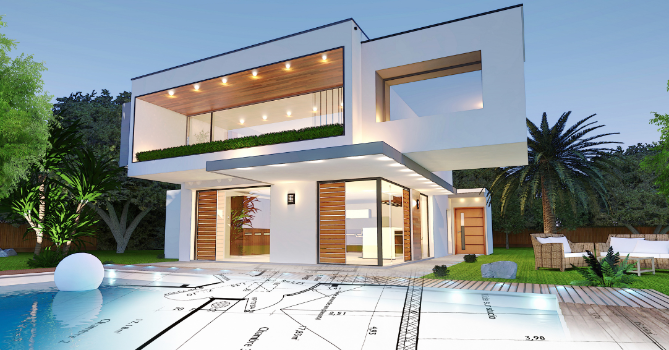
BIM also plays a critical role in offsite manufacturing. With accurate models, materials can be fabricated with exact measurements, leading to less waste. By controlling every detail, BIM ensures that the right amount of materials is used, cutting down on excess and unnecessary costs. Additionally, BIM improves material tracking, ensuring that every component arrives onsite when needed, avoiding costly delays.
Several real-world projects highlight BIM’s impact on modular construction. For example, in large-scale housing developments, BIM has helped teams finish buildings months ahead of schedule by optimizing prefabrication workflows. Hospitals and schools have also benefited from BIM’s ability to streamline complex modular designs, allowing for faster builds without compromising quality.
By integrating BIM into modular construction, teams can build faster, more efficiently, and with greater accuracy. These benefits make BIM essential for modern prefabrication projects.
Improving Collaboration and Communication Through BIM
Building Information Modeling (BIM) provides a powerful platform for improving collaboration and communication in modular and prefabrication construction. By using a shared data environment, BIM allows stakeholders—such as engineers, contractors, and manufacturers—to work together in real time. This shared access to project data means that any changes or updates are instantly visible to the entire team. As a result, everyone stays aligned, which significantly reduces the risk of miscommunication.
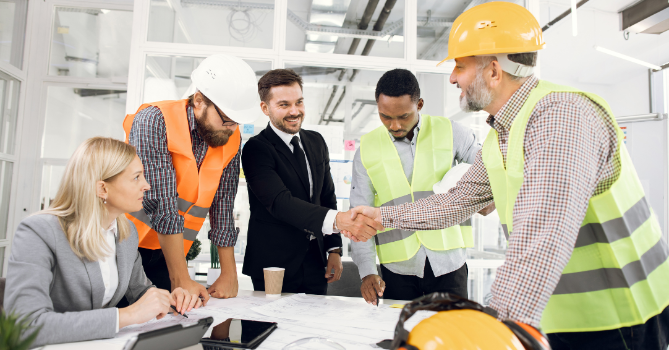
BIM also helps teams communicate more effectively by centralizing all project information. Whether it’s material specifications or design updates, every detail is stored and accessible through the BIM model. This transparency helps reduce costly errors and prevents delays that often occur due to outdated or misinterpreted information. For example, in large-scale modular projects, BIM has been shown to reduce project rework by up to 30% due to better coordination across teams.
Case studies have confirmed BIM’s role in enhancing collaboration. A modular hospital project, for instance, saw a 20% reduction in construction time because all stakeholders could collaborate seamlessly from the design stage to final assembly. This level of coordination is crucial for modular projects, where the success of offsite manufacturing depends on clear, consistent communication between all parties involved.
Cost and Time Savings with BIM in Prefabrication
BIM plays a key role in reducing both the cost and time of modular and prefabrication projects. By optimizing the design and planning phases, BIM ensures that every detail is considered before construction begins. This means fewer errors, less rework, and shorter project timelines. Prefabrication, driven by BIM, allows for components to be manufactured offsite with precision, speeding up the overall process. With better upfront planning, projects experience fewer delays, and teams can meet deadlines more consistently.
When it comes to cost savings, BIM’s ability to reduce waste is significant. Accurate 3D models ensure that only the necessary amount of materials is used, cutting down on waste and lowering costs. Additionally, labor costs are reduced as teams spend less time correcting mistakes and waiting for materials.
One example is a modular office building project that cut its construction time by 30% by using BIM to streamline prefabrication. The project not only finished ahead of schedule but also saved hundreds of thousands of dollars in material and labor costs. These real-world applications show how BIM is transforming prefabrication into a faster, more cost-effective process.
The Future of Modular Construction with BIM
The future of modular and prefabrication construction looks even brighter with the continued advancements in BIM technology. As BIM evolves, it’s becoming more powerful in automating design and construction tasks. One of the key trends emerging is the integration of AI with BIM. AI can analyze data from previous projects and use it to optimize new designs, further reducing errors and speeding up the construction process.
Looking ahead, BIM will play a major role in making modular construction more efficient and scalable. Projects using BIM and AI could see time reductions of up to 50% in the coming years.
This forward-thinking approach, combining BIM and AI, will revolutionize how we approach modular construction. Faster builds, fewer errors, and lower costs are just the beginning. As technology continues to advance, BIM will remain at the forefront, driving the growth of modular construction and shaping the future of the industry.
Conclusion: Embrace BIM for Faster Modular Construction
Leveraging BIM for modular and prefabrication construction offers undeniable benefits. It leads to faster builds, reduced costs, and fewer errors throughout the project. By integrating BIM into their workflows, companies can streamline their construction processes and increase overall efficiency.
Now is the time for businesses to embrace BIM for their upcoming projects. Its ability to optimize prefabrication and improve collaboration will set companies apart in a competitive industry. As BIM continues to evolve, it will play a key role in redefining construction efficiency, making it the cornerstone of future builds.