.png)
Enhancing Predictive Maintenance with BIM and Smart Sensors
Introduction
The construction industry is evolving fast. Advanced technologies like Building Information Modeling (BIM) and smart sensors are reshaping how we approach maintenance. Predictive maintenance is no longer just a concept; it's becoming the standard. By integrating BIM and smart sensors, building managers can predict issues before they happen. This means fewer breakdowns, reduced costs, and smoother operations.
BIM provides a detailed digital view of a building’s systems. Smart sensors collect real-time data on equipment and conditions. Together, they create a powerful tool for tracking and managing assets. This combination helps identify problems early and keeps buildings running efficiently.
This article will explore how BIM and smart sensors work together for predictive maintenance. We'll discuss their impact on efficiency, cost savings, and sustainability. With these tools, construction and facility management can move towards smarter, more proactive practices. The future of maintenance is here.
Understanding Predictive Maintenance
Predictive maintenance is all about staying ahead of problems. It monitors equipment in real time to catch issues early. Instead of waiting for something to break, this approach predicts when maintenance is needed. This prevents unexpected failures and reduces costly downtime.
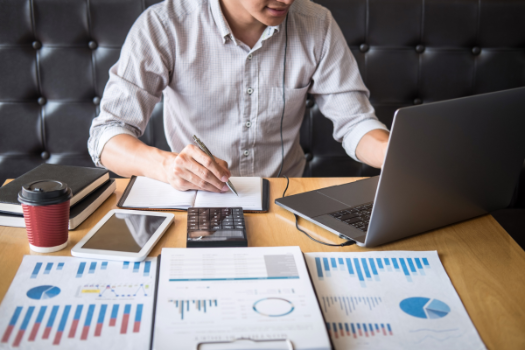
Traditional maintenance methods rely on fixed schedules or reacting to breakdowns. Predictive maintenance, however, uses data analytics to identify patterns and predict future issues. This means equipment gets serviced only when necessary, saving time and resources.
In modern buildings, unplanned outages can disrupt operations and lead to big expenses. Predictive maintenance helps avoid these risks. By keeping equipment in top condition, it ensures smooth operations and longer asset life.
This approach is becoming a must-have in facility management. It’s efficient, cost-effective, and helps businesses stay one step ahead. Predictive maintenance isn’t just smart—it’s the future of building management.
The Role of BIM in Maintenance
Building Information Modeling (BIM) is like a digital blueprint for buildings. It shows not just how a building looks but how it works. BIM captures detailed information about every component, from walls to wiring. This makes it a powerful tool for managing maintenance.
With BIM, facility managers can see the current condition of assets in one place. It helps track maintenance histories and plan future repairs. Instead of guessing or relying on paper records, managers can use BIM to make informed decisions. This saves time and reduces errors.
BIM also improves communication. Maintenance teams can share updates and access the same data in real time. This keeps everyone on the same page. By streamlining maintenance tasks, BIM ensures that activities are well-organized and documented.
In today’s fast-paced construction world, BIM is a game-changer. It turns maintenance into a smarter, more efficient process.
Integration of Smart Sensors for Real-Time Data Collection
Smart sensors are transforming how buildings are monitored. These small devices gather real-time data on key factors like temperature, humidity, and equipment performance. They provide constant updates on how a building is functioning.
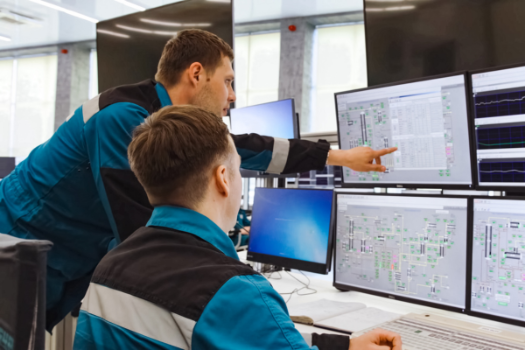
When smart sensors are integrated with BIM, their power grows. BIM acts as the central hub where all this data comes together. Facility managers can monitor building conditions continuously and identify problems early. For example, if a sensor detects unusual vibrations in machinery, it can alert the team before a breakdown happens.
This integration makes maintenance more proactive. Instead of reacting to failures, teams can address issues before they escalate. It also reduces unexpected downtime and extends the life of equipment.
Smart sensors and BIM create a system that is always watching, analyzing, and improving. Together, they bring precision and reliability to building management, ensuring smoother operations and fewer surprises.
Implementation Strategies
Implementing predictive maintenance with BIM and smart sensors requires a step-by-step approach. Here’s how to get started:
Assess Existing Systems: Begin by evaluating your building’s current infrastructure. Determine if it can support the integration of BIM and smart sensors. This step identifies gaps and ensures a smooth transition.
Deploy Sensors: Choose and install sensors that monitor critical parameters like temperature, humidity, and equipment performance. Ensure the sensors are compatible with your existing systems to avoid integration issues.
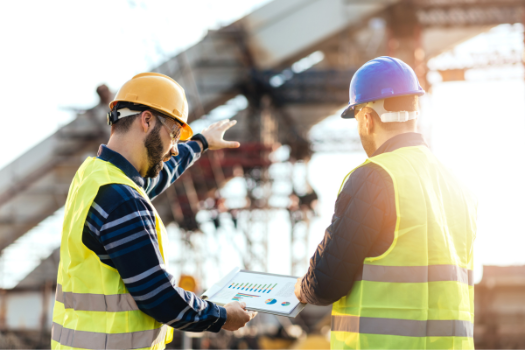
Update BIM Models: Incorporate sensor data into your BIM models. This creates a unified platform where real-time data and digital building information come together. It’s essential for effective monitoring and analysis.
Use Data Analytics: Analyze the data collected by sensors to identify trends and predict maintenance needs. Advanced analytics tools can detect patterns that humans might miss, enabling faster and smarter decisions.
Monitor and Improve Continuously: Maintenance doesn’t stop after implementation. Regularly review the system’s performance and update strategies based on new insights. This ensures long-term optimization and adapts to evolving building needs.
By following these steps, you can fully leverage BIM and smart sensors for predictive maintenance. The result is a smarter, more efficient building management system.
Benefits of Combining BIM and Smart Sensors for Predictive Maintenance
The combination of BIM and smart sensors brings numerous benefits to predictive maintenance. These technologies work together to make building management smarter and more efficient.
Enhanced Data Accuracy: Integrating real-time sensor data into BIM models provides a clear and detailed picture of asset conditions. This precise information helps managers make better maintenance decisions, reducing guesswork and errors.
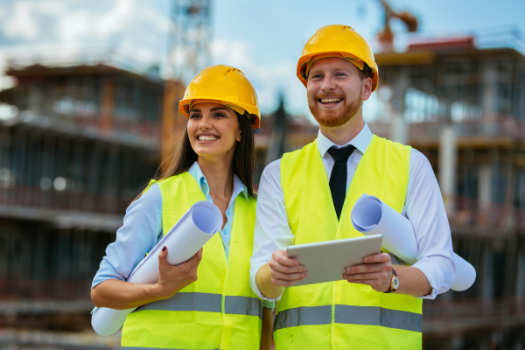
Improved Maintenance Scheduling: Sensor data feeds predictive analytics tools, enabling maintenance to be planned based on actual equipment conditions. This means no more unnecessary servicing or missed repairs. It optimizes resource use and keeps systems running smoothly.
Cost Reduction: Preventing unexpected failures reduces downtime, which can be costly and disruptive. With predictive maintenance, problems are addressed before they escalate, saving organizations both time and money.
Extended Asset Lifespan: Regular maintenance based on accurate data ensures equipment stays in good condition for longer. This not only minimizes replacement costs but also supports sustainable building practices.
BIM and smart sensors create a system that is proactive and efficient. They reduce risks, cut costs, and extend the life of building assets. By combining these technologies, facility managers can achieve a higher level of control and reliability in building maintenance.
Challenges and Considerations
While combining BIM and smart sensors brings many advantages, it also comes with challenges that need careful attention.
Data Management: The integration generates massive amounts of data. Managing this effectively requires advanced data systems to ensure accuracy and reliability. Without proper tools, data can become overwhelming and less useful.
Interoperability Issues: Different systems and technologies must work seamlessly together for integration to succeed. This includes ensuring that sensors, software, and BIM platforms can communicate effectively. Compatibility issues can slow progress and create inefficiencies.
Initial Investment Costs: Setting up these systems can be expensive. The cost of sensors, software updates, and training adds up quickly. Organizations need to assess the potential return on investment to justify these initial expenses.
Despite these challenges, the benefits often outweigh the hurdles. With proper planning and a focus on long-term gains, businesses can overcome these obstacles and unlock the full potential of BIM and smart sensors for predictive maintenance.
Conclusion
The integration of BIM and smart sensors is transforming predictive maintenance in construction. This powerful combination boosts efficiency, reduces costs, and ensures building assets last longer. By using real-time data and proactive strategies, organizations can prevent failures before they occur. This approach not only minimizes downtime but also supports sustainability goals. Adopting these technologies enables businesses to better manage their facilities and create safer, more reliable environments. As the construction industry continues to evolve, BIM and smart sensors stand out as essential tools for smarter, more sustainable building management. The future of maintenance is here—proactive and data-driven.